革新の分岐点 ~製品ライフサイクルに対応する持続可能なサポートと業務変革~
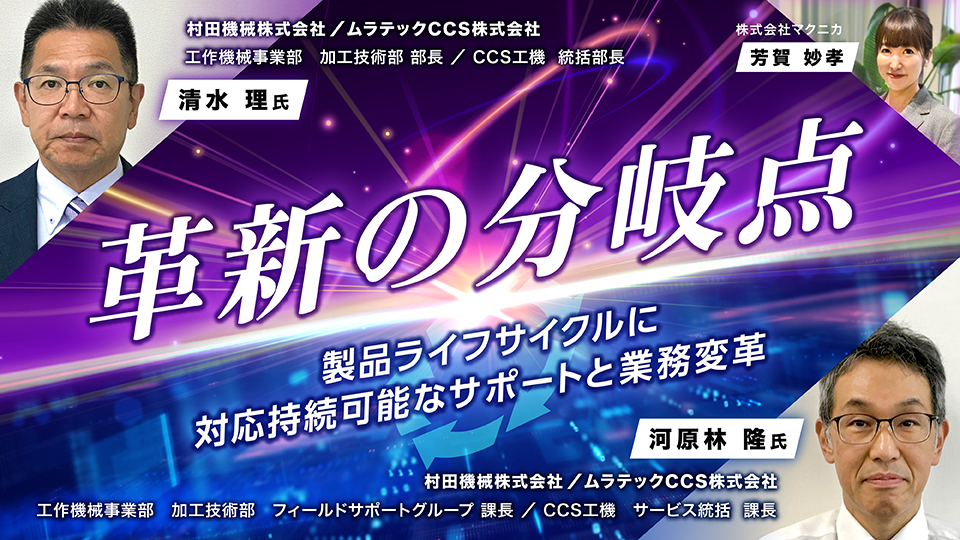
FAの総合メーカーである村田機械株式会社(ムラテック)は、繊維機械や工作機械の製造販売を事業の柱に、技術力の高さでいくつもの業界に変革をもたらしてきました。サービスエンジニアリングを担うグループ企業のムラテックCCS株式会社との二人三脚で、高品質なアフターサービスを顧客に提供しています。この度、マクニカの支援のもと、AIを利用したリモート診断システム「プライマリドクタサービス」を開発し、2024年11月から提供を開始しました。本記事では、持続可能なサポートと業務変革を実現するために取り組んだプライマリドクタサービスのプロジェクトついて、同社の清水様と河原林様にお話をうかがいました。
【講演者】
![]() ![]() |
![]() |
【目次】
・高品質なアフターサービスをいかに継続するか
・プライマリドクタプロジェクトに取り組む
・3チーム体制で小さなPDCAを高速に回す
・稼働データのAI診断で故障前に対処して稼働率向上
高品質なアフターサービスをいかに継続するか
芳賀:村田機械様は「社会や時代をよりよい方向に変える『革新の分岐点』でありたい」を企業スローガンに掲げていらっしゃいますね。
清水:はい、私達は常に新しい技術を創造し、お客さまに喜ばれる製品の提供を通じて、社員1人ひとりの幸せと豊かな社会の実現を目指します。この想いがグループ全体での事業の柱となっています。
芳賀:村田機械様はこれまでの歴史のなかで、革新的なイノベーションを起こしてきましたが、具体例を教えていただけますか。
清水:その代表的な製品が2つあります。1つ目は繊維機械のマッハスプライサーです。従来の織物は糸の繋ぎ目が欠点でした。当社のマッハスプライサーは繋ぎ目なくすことができる画期的な発明でした。1983年の製品ですが、現在も世界の業界スタンダードとなっています。
2つ目は工作機械のガントリーローダです。自動車産業において、多品種の量産物を加工する際、従来のシーケンス制御ではなく、C言語を使用した制御を可能としました。使い勝手が良くて汎用性が広く、かつ、他社の追随を許さない高速の自動搬送ができます。
芳賀:まさに革新の分岐点となるイノベーションではないでしょうか。それら、もの作りの現場を支える工作機械は、アフターサービスも大切ですよね。
清水:おっしゃるとおりです。当社ではCCS工機という部門が主体となり、点検・補修サービスや移設、コールセンター、レベルアップスクールなどのアフターサービスを通して、世界中のお客さまをサポートしております。
芳賀:技術の進歩によって工作機械の寿命が延び、お客さまが機械を長期間使用するケースが増えています。あるシミュレーションによれば、アフターサービス対象の機械は2024年に比べて、2045年には約1.5倍に増えると予測されています。
村田機械様の製品も、30年以上など長期間にわたり使用しているお客さまが多いとお聞きしています。アフターサービス対象の工作機械が増えると、担当者の人員も増やす必要がありますよね。
清水:それは私達も大きな課題と認識しております。当社の工作機械は約10年を経過すると徐々に故障箇所が目立ち始めるのですが、従来はお客さまから故障のご連絡をいただいて、現地にサービスマンを派遣するスタイルでした。1万5000台超の製品が稼働するなか、昨今の人手不足、働き方改革に伴う労働時間減少も加わり、当社のアフターサービス部門だけでは、人手による点検保守が限界を迎えつつありました。
芳賀:これは業界全体の課題と言えるでしょう。実際に現場でアフターサービス業務に従事している皆さまは、どう感じていますか。
河原林:現場のフィールドサービス担当者は皆、日々頑張っていて、お客さまからも非常に高い満足度をいただいております。ただ、今後増え続けるメンテナンス対象機に対して、これまで通りの高品質のサービス提供の継続は困難になると考えています。それゆえ、今の時点から新たな体制を作ることが不可欠なのです。
プライマリドクタプロジェクトに取り組む
芳賀:こうした課題に対して、「プライマリドクタプロジェクト」に取り組まれました。まずはプロジェクトの概要をお聞かせください。
河原林:お客さまが使用されている主に10年以上経った古い工作機械に対して、突然のマシンダウンによって損失することなく、効率的に加工できるよう支援することを目指しています。従来はお客さまの機械が故障してから連絡をいただいて対応する事後メンテナンスです。これを故障前に部品を交換するなどの計画メンテナンスに変革することで、お客さまの設備稼働率アップによる生産性向上、および当社担当者の労働環境改善やモチベーションアップを図ります。
清水:困難なプロジェクトですが、お客さまも当社担当者も満足を高められるので、非常にやりがいのある仕事ですね。
河原林:本プロジェクトでは、ミッションとビジョンを言語化して、プロジェクトメンバーの目標と方向性を一致させました。ミッションは「データ分析による予防保全への変革を行い、サービス活動の新時代を切り拓く」です。ビジョンは「〝オンコール対応から予知保全へ" 機械を停止させない新たなサービスを先駆けて提供できる企業を目指す」です。データ分析による予防保全は、まさに私達サービス部門にとっての革新の分岐点である考えています。
芳賀:アフターサービスに大きな変革をもたらしますよね。本プロジェクトは実に多くの方々が携わっていますが、チーム体制を教えていただけますか。
河原林:お客さまと接するサービス部門がプロジェクトオーナーを務めています。事業部開発部門では技術的な開発と検証を行い、製造部門へはユーザー視点の意見や過去の経験から得たナレッジを共有いただき、お客さまにはデータ収集にご協力いただき、サービス開発に活かしていきました。これら3部門とお客さまが密に連携してプロジェクトを進めています。
芳賀:サービス部門と工作機械事業部に加え、ユーザー視点を持った製造本部も一緒であることに私はインパクトを受けました。
河原林:製造本部からは、点検表の見やすさや実際に現場が必要としているサービスなどのアドバイスをいただきました。
3チーム体制で小さなPDCAを高速に回す
芳賀:今回のプロジェクトは発足からサービスインまでが短く、かなりスピーディでしたが、何か意識された点はありましたか。
河原林:プロジェクトを進めるにあたり、「機能開発」「サービス開発」「データ分析」と3つのテーマを掲げました。そして、各テーマでPDCAサイクルを回すことでサービスを開発しました。その際、小さなPDCAを高速で回すことを強く意識し、さらに途中の段階で定期進捗共有会を実施。経営層や他部門からアドバイスをもらい改善を繰り返してきました。
清水:定期進捗共有会には副社長以下、工作機械事業部の執行役員、製造本部の本部長が毎回必ず参加し、細かいところまでアドバイスをもらうなど、大変有意義な会でした。現場メンバーの励みにもつながり、最終的にはプロジェクトの成功に大きく寄与しました。
芳賀:私は、本プロジェクトはDXプロジェクトであると認識していましたが、清水さんからは、違うのではないか?と言われたことがありました。
清水:はい、発足当初はDXを全く意識していませんでした。10年を超える工作機械の多くがお客さまの現場で稼働しており、故障が発生したら出向いて修理復旧するという業務を長年繰り返しきたなかで、工作機械からデータを収集して、異常が発生している箇所をお客さまにレポートできないか、といった考えから、このプロジェクトを開始しました。
その途中でAIを活用している当社の部署の協力を得て、集めたデータをAIで解析してもらうことになり、その結果としてプライマリドクタのサービス化に至りました。関係部門から多大なサポートが得られ、チーム一丸となって開発にまい進したことが、DXにつながったのでしょう。
芳賀:経産省によれば、DXとはデジタル技術やツール導入自体ではなく、データやデジタル技術を使って顧客目線で新たな価値を創出していくこと、そのためにビジネスモデルや企業文化などの変革に取り組むこととされています。
本プロジェクトはメンバーの皆さんが、本当にお客さまが必要としているものは何なのか、業務プロセスがどう変わるのかなど、顧客価値を最初から最後まで熟考し続けていたことが素晴らしいと私は考えています。加えて、サービス提供側である村田機械様の業務プロセスがどう変わり、どんな価値が生まれるのかも真剣に考え抜き、変革が起こったのでしょう。
河原林さんは今回のプロジェクト振り返って、どの点が良かったとお考えでしょうか。
河原林:3チーム体制を取ったことですね。お客さま価値を重視してサービス内容を検討するチーム、各種データを分析して仮説立案などを行うチーム、必要な機能を開発するチームが協力しながら連動し、さまざまな課題に同時並行で取り組み、方向性を短期間で決定できました。
特にサービス内容検討の部分では、懇意にしている複数のお客さまにご協力していただけ、お客さまの現場でテストできたのが大きかったですね。それによって、検証を適切かつ迅速に進められました。
稼働データのAI診断で故障前に対処して稼働率向上
芳賀:ここで改めて、プライマリドクタサービスの概要を教えていただけますか。
河原林:お客さまが長年使用している工作機械の稼働中に、データを収集し、AIで診断します。故障や品質異常が発生する前の適切なタイミングでメンテナンスを実施することで、さまざまなロスを減らし、お客さまの生産性向上を支援するサービスです。
データ収集機器はお客さまの手で簡単に脱着できます。収集するデータは主に加工軸や搬送機器の状態です。3日間データを取得し、AIで診断をしてレポートを提出します。そこで異常が見つかれば、別途、人手による点検を実施し、必要に応じてオーバーホールします。
芳賀:お客さまからすれば、メンテナンスは必要だけど、機械をなるべく停止したくないという課題があります。その点、プライマリドクタサービスは止めずに点検できるため、そういった課題解決に最適ですよね。
河原林:そうですね。お客さまは他にも、突発的なマシンダウンは避けたい、メンテナンス費用を抑えたい、故障・修理などによるイレギュラーな残業は避けたいといった課題を抱えています。プライマリドクタサービスはそれらの課題解決にも有効であり、安定稼働による稼働率向上を実現するサービスになっています。
芳賀:ユースケースをご紹介いただけますか。
河原林:2つご紹介します。1つ目は、故障時にはメーカーへ連絡し、設備復旧を依頼されるお客さま、および故障の予兆に気づくことが難しいお客さまのケースです。プライマリドクタサービスを利用すれば、故障前の診断や点検によって、突発的な故障を回避できます。
2つ目は自社内の保全体制が充実しており、修理経験が多くて知識が豊富なお客さま、および修理の必要可否の判断根拠となるデータを必要とするお客さまのケースです。プライマリドクタサービスの診断結果を用いれば、修理の必要可否をより的確に判断可能となり、計画修理につなげられます。
芳賀:最後に清水さんから一言いただけますか。
清水:我々サービス部門の責務は、お客さまの設備が導入から廃却までの期間、安定的な機器稼動を提供することです。今後労働人口が減少しても、高品質なサービスを継続可能とするためにプライマリドクタサービスを開発しました。また、今後開発される機器に関しても、今回のプライマリドクタのノウハウを役に立て、さらにブラッシュアップをして開発を続けていきたいと考えております。
芳賀:本日はありがとうございました。