これからはじめる「製造業DX」 ~製造業の課題・DXのメリット・事例を知る~
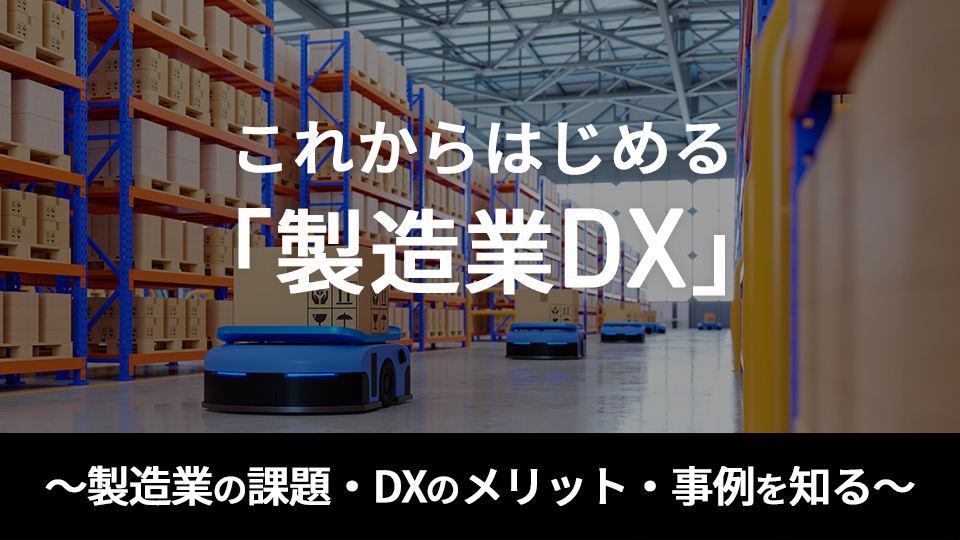
「ものづくり大国」とも呼ばれるドイツが、製造業の高度化を目指すため2013年に構想した「Industrie(インダストリー)4.0」。時の流れは早いもので、2023年でそれから10年目を迎えました。
また日本ではDXが広がる契機になったとも言われている、「デジタルトランスフォーメーション(DX)を推進するためのガイドライン」を、2018年12月に経済産業省が公表しました。
いま皆さんの会社では、DXは進んでいるでしょうか。あるいは、これから本格的に取り組まれるのかもしれませんね。
昨今では日本も含む世界中で、様々なDXの事例・実績を観測できるようになってきました。マクニカとしてはこの潮流を後押ししつつ、さらなるDXの普及に貢献していきたいと考えています。
そこで本記事ではマクニカが携わる事業のひとつである、製造業DXの基礎や取り組むメリット、事例などをご紹介します。今回の内容はいわゆる"入門編"的なものとなりますが、本記事を通じてDXに携わる方が1人でも増えれば、たいへん嬉しく思います。
目次
製造業DXとはなにか?
そもそも、「製造業DX」とは一体なんなのでしょうか。
まず、大まかには「業務変革・新事業創出などを、デジタル技術を使っていち早く実現すること」とまとめられるでしょう。一方、実作業レベルで考えた場合には下記が重要であると言えます。
■多くの業務の現状や目指すべき姿をイメージしながら、ローコードやアジャイル開発といった手法を駆使し、いち早く体験を行うこと
■人・モノ・手法・設備などのさまざまな情報をデータで管理しつつ、AIなどの最新技術を使い、業務を効率化すること
つまり製造業DXは、個人のスキルや人脈などに紐づいている業務のプロセスや、目に見えにくい情報を数値(データ)化し、かつ生産性の向上・コスト削減・品質管理・予知保全などに役立てられる一面をもっている、ということです。
このように、「データや業務の標準化/デジタル化による効率化」も、製造業DXを構成する重要な一因であることは確かです。しかし、そもそもDXにおける重要なポイントは「デジタル"トランスフォーメーション"」の名が示すように、"変革"にあります。
そしてマクニカは、「製造業DX=経営革新」とも考えています。
もう少し噛みくだくと、「標準化/デジタル化で業務や新しい事業(施策)の検討プロセスを効率化しつつ、最終的には"人が行うべき仕事"にフォーカスし、会社全体のビジネスモデル変革を目指す」......ということになります。
この「ビジネスモデル変革」には、もちろん既存事業のカイゼンも含まれます。ですがそのうえで目指したいのは、自社の強み(ケイパビリティ)を活かしつつ、市場/環境の変化も見越して新規事業の創出をしたり、メイン(コア)となる事業を強化して新規顧客を開拓したり価値を生み続ける仕組みを作ることです。
いずれも簡単に為せるものではありませんが、そもそもDXは中長期的視点で取り組む施策であるため、まさに事業のあり方や進め方を見直す絶好の機会でもあると言えます。
また、マクニカは製造業DXにおいて「プロジェクトの中核は"人"」というポイントも非常に大切にしています。
その理由は「DXの推進には経営層も含めた社内のあらゆる組織・事業部の垣根を超えた連携が必要不可欠であり、その状態を作り上げられるのがやはり人だから」です。
DX推進時のよくある失敗例として挙がるのが、「とりあえずAIなどの最新技術を導入してみる」というものです。
かつてはマクニカもこの罠に陥り、お客様に適切なご支援が中々できずに苦心した時期がありました。ですが、2013年から積み上げてきた経験の末、ようやく答えにたどり着くことができたのです。
つまり製造業DXにおいては、「会社をより良くしたい」という熱い想いをもって舵取りができる推進担当者が必要不可欠であり、かつ各社員もDXの意義を正しく理解し、会社全体が一丸となって取り組むことが重要なのです。
これが「プロジェクトの中核は"人"」であるということと、マクニカの考える製造業DXの本質です。
日本の製造業における課題とDXのメリット
現代における日本の製造業は、様々な課題に直面しています。そして製造業DXはそれらの突破口であるとともに、先述のように業務効率化を図る手段として期待されています。
そこでこの項では、製造業DXの必要性をより理解すべく、日本の製造業における課題やDXによるメリットをまとめました。
日本の製造業における課題
まず、主な課題を整理してみました。
【課題①:少子高齢化にともなう労働人口の減少】
少子高齢化が進むと、人材の確保が困難になる。製造業はライン作業や目視検査などに人力を必要とするケースがまだ多いため、人手不足による影響が大きいとみられる。
【課題②:属人化によるノウハウ継承の壁】
現場が特定の技術者の「経験」や「カン」などを軸にした業務に依存していたり、そのノウハウの継承が困難だったりする場合、新戦力が育たない。
【課題③:海外製品の台頭】
日本の製品は品質の良さがウリだが、昨今では低コスト&高品質な海外製品も増えており、強力なライバルと化している。また、それにともないユーザーの価値観も多様化しており、従来どおりの運用ではニーズに対応しきれない可能性も。
【課題④:不確実性の時代】
コロナ禍や特定地域の紛争など、世界中に大きな影響を与える事象が立て続けに起こり、材料調達~販売&消費の工程(サプライチェーン)などがそのあおりを強く受けている。
いずれも見過せない要素ではありますが、特に【課題①:少子高齢化にともなう労働人口の減少】や【課題②:属人化によるノウハウ継承の壁】については、身近なところでお悩みの方も多いのではないでしょうか。
もし上記のような課題を解決したいと強く感じているのであれば、DXを推進する価値は十分にあると言ってよいでしょう。
DXによるメリット
次に、DX推進によって得られる主なメリットをまとめました。
【メリット①:データ可視化】
受注・生産・アフターケアといった各工程を円滑に進めるための情報や、設備の状態などを可視化したうえで、データとして一元管理できるようになる。集めたデータは需要に応じた生産体制の調整や、販売予測の策定などにも役立つ。また技術者のもつノウハウをデータとして可視化し、社員に幅広く共有することで、属人化の防止に期待がもてる。
【メリット②:生産性向上】
製造現場の自動化、在庫管理や出荷記録管理の効率化などにより、生産性向上および、ヒューマンエラーによる生産ロスの軽減を見込める。また、これらによって必要なマンパワーが少なくなれば、人手不足の対策になる。
【メリット③:クオリティ安定】
微細な調整が必要な作業を機械作業化できれば、製造物のクオリティを安定させられる。恒久的な品質保全は顧客からの信頼につながり、対海外製品も含む競争力強化になる。
【メリット④:コスト削減&リソース最適化】
単純な作業を機械任せにすることで、人件費や生産コストの削減を見込めるほか、技術者がよりクリエイティブ(高度)な業務に従事できる。また、人手不足の対策にもなる。
総じて、DXの推進においては「データ可視化」がカギを握っているため、最初はこの分野から情報収集をするのがよいでしょう。
なお、仮に作業の自動化をするだけならデータは不要かもしれませんが、あくまで大切なのは「自動化をすること」ではなく、「DXの先に何を成し遂げたいか」という"目的"です。
また、扱うデータも闇雲に取得すればいいというものでもありません。「目的を達成するためにはどんなデータが必要か」「そのデータはどうやって取得するのか」などを丁寧にひとつひとつ紐解いていくことが、製造業DXを実現するための秘訣です。
事例紹介
この項では、実際にマクニカが共創させていただいたお客様の事例をピックアップしてご紹介します。
データ可視化でExcel管理から脱却! ~東洋新薬様~

1つ目は、東洋新薬様の事例です。
東洋新薬様は「HIGH-END VALUE」の企業理念のもと、健康食品・化粧品のODM(※1)・OEM(※2)を合わせた「ODEM」を武器に、第一線で事業を推進しています。
※1:Original Design Manufacturing。委託者のブランドを用いたうえで、製品の設計・デザイン・生産などの幅広い業務を担当すること。
※2:Original Equipment Manufacturing。委託者のブランドを用いたうえで、製品の生産のみを担当すること。
業績が右肩上がりの成長を続ける一方で、東洋新薬様は転換期を迎えていました。
それまでは営業部門・品質保証・研究開発分野それぞれで単機能のシステム構築を行ってきたのですが、さらなる成長のためには生産管理システムも含めた基盤全体の刷新が必要であり、それを実現する手段がDXの強力な推進だったのです。
全社的にDXが推進されるなか、新たに竣工した工場は「設備稼働率を最大化する」をテーマのひとつに掲げていたのですが、その実現には複数の課題がありました。
【課題①:進捗状況の可視化】
製造ラインの進捗状況が、十分に可視化できていなかった。製造部門の担当者が現場に張り付きながら改善を続けることで稼働率を相当レベルに高めることはできたが、事業が拡大してライン数が増えれば、その方法がすぐに破綻することは分かっていた。
【課題②:リアルタイムな稼働状況の把握】
Excelで稼働状況などの管理をしており、データも自分たちで収集していたが、その場で分析して処置するまでには至っていなかった。また、収集したデータは当日の作業終了後に集計を行う必要もあった。
【課題③:営業から製造までのデータの一気通貫】
工場全体の作業を行う製造統括部門に関してはデータ自体が見えておらず、現場から距離が離れてしまうほど状況把握が困難な環境だった。本来は製造の出来高に応じて検査部門や物流部門に至る工程への連携が必要だが、それも不十分。受注生産となるODEMが中心の同社にとっては、営業から製造まで一気通貫でデータを流す必要があった。
まさに、「製造業あるある」と言ってもよい内容ではないでしょうか。
そして東洋新薬様はこれらを解決すべく、マクニカと共に動き始めました。
【取り組み:リアルタイムなデータ収集と可視化】
包装後の重量検査実績・充填機の実績・NG商品数の歩留まり・包装箱の不良(ロス)などのデータをリアルタイムで収集して可視化。稼働目標に対する達成率なども含め、ラインや事務所の大型モニターで一目瞭然になった。また、Excelによるデータ集計も不要に。
今後は製造の遅延があった場合に、迅速に対応するための材料としても活用できるはず。最初は特定ラインをモデルとしたが、最終的には工場全体への展開を念頭においている。
東洋新薬様は、経験の有無に関わらず誰にでも異常が認識・判断できることを重視していました。また、歩留まりなどの数字を常時見える化することは現場の意識を高め、改善活動につながっていくような循環を生み出せると考えていたそうです。
ほかにも、「スマート工場(製造業DX)の第一歩を踏み出せたことが最大の効果」「最終的には基幹システムとの連携で、営業から物流までがしっかり連動しながら見える化した情報を活用し、具体的な効果につなげることで、次のステップで実装する機能に活かしていきたい」などのお声も担当者様からいただきました。
このケースの分かりやすいところでは、まだまだ現場に多いと思われるExcelによるデータ管理からの脱却も、工数削減などの面で大きな一歩だったと言えるでしょう。
この事例を詳しく見る
AI活用で、1日がかりだった新人の業務が数分に短縮!? ~コイワイ様~
2つ目は、株式会社コイワイ様の事例です。
同社は「鋳造技術の伝承発展に努めものづくりを通じて社会に貢献し価値ある企業として歴史を刻む」を理念とし、試作・量産鋳物・金属粉末積層部品の製造販売を手がけています。
鋳物事業では業界に先駆けて3Dプリンタによる試作製造に取り組み、特定の工程を省略することで工期を大幅に省略するなど、今日のDXにつながる革新的な挑戦を積極的に行っていることが特徴です。
そんな同社は、近年では主力事業の自動車関連以外に、建設機械・ロボット・医療機械など様々な業界へ販路拡大を図ってきました。おかげで試作事業における相談件数はみるみると増えていったのですが、結果として、下記のような課題が浮き彫りになりました。
【課題①:若手の人材不足と、熟練者の技術継承】
経験豊富な熟練者が中心の職場で、新人が学べる環境が十分に整備できておらず、新たな人材の獲得や技術の継承も含めた環境づくりが急務に。
【課題②:見積作成のスピードと精度の向上】
試作事業は量産前の顧客からの要求が千差万別であるため、見積作成時に過去の知見や実績などを踏まえながら、金額を算出する必要がある。案件の増加により迅速な対応が必要な状況のなか、ベテランは1~2時間で完了できるが、新人だと1日がかりになることも。結果、時間がかかりすぎたり見積精度が低いことが原因で、受注を逃すケースもあった。
昨今では「すぐに見積が欲しい」という顧客も増えていたため、新人であっても、できる限りブレの少ない見積を短時間で作成できることが必要だったそうです。
そこでコイワイ様は、マクニカと共に下記のような取り組みをしました。
【取り組み:過去データから類似検索ができるシステムを構築】
AIを活用した3Dデータ類似検索システムを構築し、特定の部品だけで見ても累計で1万点以上を検索可能になった。これにより、誰でも数分のうちに類似品を探し当てられるようになることが期待される。
従来は見積作成から検査出荷までに17日必要だったが、これを7日まで短縮することが将来的な目標と設定された。
なおコイワイ様からは、「本件で採用したAIは見積作成以外の管理工程にも転用できるなど、様々な場面の時間短縮につなげていける見込みがある」という評価もいただきました。
このように享受できるメリットを「点」ではなく、「線」でつなげていけることもまた、製造業DXの魅力だと言えるのではないでしょうか。
コイワイ様は今後、最終的に鋳造方案の作成に至るプロセス全体の工数削減を通じ、顧客に対して高い精度の見積を迅速に提供し、ビジネス機会をさらに拡大させていきたいとのことです。
この事例を詳しく見る
まとめ
今回は、日本の製造業における課題・DXのメリット・事例などをお伝えしました。
DXと言うと、「ただちに大規模な取り組みをしないと......」と不安になる方もおられるかもしれません。しかし、東洋新薬様が特定のラインに限定したデータの可視化からスタートしたように、まずはピンポイントなところから始め、第一歩を踏み出すだけで世界が変わるケースもあるのです。
またコイワイ様の事例はAIによって工数が大幅に短縮され、さらに当初の想定範囲以外の業務効率化にも期待がもてるなど、メリットを広範囲に享受できた好例であり、DX推進の重要性が垣間見えたかと思います。
製造業DXの夜明けは、まだまだこれからです。
この記事が「DXを推進したい」と強く願う方々にとって、きっかけのひとつになれば幸いです。
■マクニカ DIGITAL SYNERGY FACTORY Webサイト